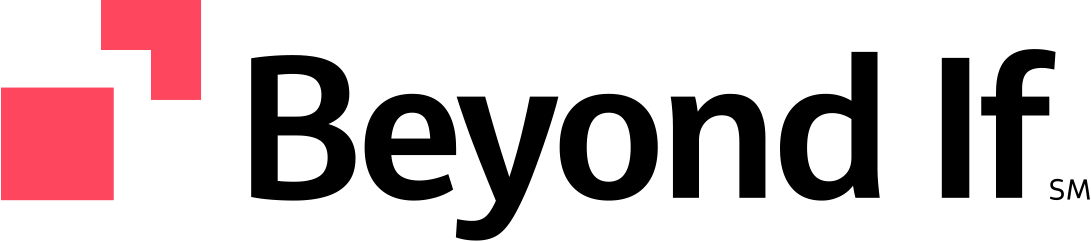
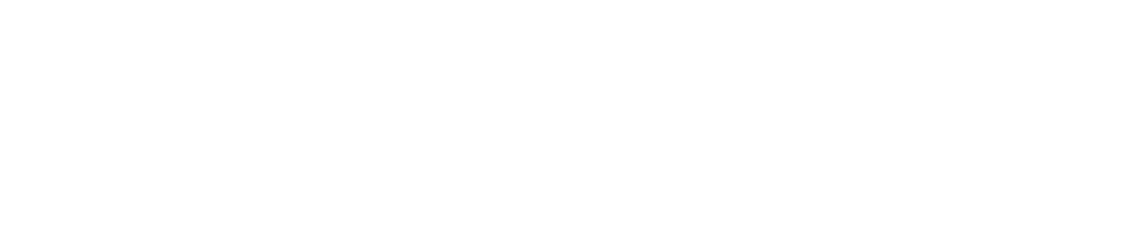
At Jacobs, we're challenging today to reinvent tomorrow by solving the world's most critical problems for thriving cities, resilient environments, mission-critical outcomes, operational advancement, scientific discovery and cutting-edge manufacturing, turning abstract ideas into realities that transform the world for good. With approximately $16 billion in annual revenue and a talent force of more than 60,000, Jacobs provides a full spectrum of professional services including consulting, technical, scientific and project delivery for the government and private sector.
For more than 70 years, our teams have provided integrated solutions to help solve the most complex and hazardous challenges of space exploration. We invent by imagining what’s possible.
A curated selection of some of the top-listened to and trending podcast episodes from our popular If/When podcast series, which has over 6M downloads to date.
Sit down with our visionary team of thinkers, dreamers and doers to see what a day in the life is like.
As our clients navigate the digital transformation and growing cyber risks, we have positioned ourselves at the forefront of this growth, adding digital capabilities, products and tools to serve a growing set of customers.
Together with our visionary partner, PA Consulting, we're establishing our position in high end advisory services, creating a springboard to expand in high value offerings beyond the core.
The only certainty about the future is uncertainty. Resilience is an attribute of a smarter planet, and requires planning and adapting ahead of potential threats. We help our clients survive, recover, adapt and thrive.
Jacobs. A world where you can.
As a purpose-led company, we know we have a pivotal role to play in addressing the climate emergency. We consider this not only good business, but our duty to channel our technology-enabled expertise and capabilities toward benefitting people and the planet.
For more than 30 years, Jacobs has been responsible for planning and implementing Lead and Copper Rule-related strategies which protect millions of people in the U.S. and Canada. Our work includes enhanced water quality monitoring strategies, sampling plan development, harvested pipe-scale analysis, lead service line inventories and replacement plans, corrosion control studies and the incorporation of equity and environmental justice considerations into compliance programs.
Jacobs is working to help clients across the United States secure federal funding for projects that make our cities and communities more connected and sustainable. Working hand-in-hand with clients from coast to coast and everywhere in between, Jacobs develops bold, innovative solutions to address the nation’s toughest challenges.
Now more than ever, we appreciate the hard work, sacrifice and dedication of the medical profession in ensuring the health and safety of our communities.
Together, we are stronger. Together, we can transform the future.
We work in partnership, delivering some of the most challenging, diverse and innovative projects and programs globally across multiple sectors. We integrate complex interfaces across planning, procurement and delivery to help unlock better social, environmental and economic outcomes from mega and giga projects.
We’ve provided design-build services to the water sector for over 25 years and delivered more than 150 projects. We offer fully integrated design-build and design-build-operate capabilities to tackle the most complex water challenges and work in close collaboration with our clients.
As climate change threatens water security around the world, more communities are turning to water reuse as a resilient water supply solution and embracing the OneWater principle that all water has value. Jacobs has been supporting clients with water reuse programs for decades, beginning with the first applications of advanced wastewater treatment technologies in the 1960s. We provide our clients with a full range of services, from water reuse feasibility studies to design, construction and operations.
Jacobs’ deep experience with advanced technology systems and our wide-ranging program support capabilities make us a premier partner at locations across the world. We deliver the right talent, tools and processes to support and enable our customers’ missions.
The National Air and Space Museum's One World Connected exhibit will tell the story of how flight fostered two momentous changes in everyday life: the ease in making connections across vast distances and a new perspective of Earth as humanity’s home. Below are some stories from Jacobs that also highlight the connections and digital solutions we are making around the world.
Stories that capture our partnerships and innovative impact for a more connected, sustainable world
Whether you change your oil every 3,000 miles without fail or rely on your smart vehicle to ask for a change when it’s ready, checking and changing your car’s oil is key to ensuring engine longevity.
The same can be said about ground support equipment and spacecraft at the NASA Kennedy Space Center (KSC) in Florida. The nation’s entryway to space, KSC has served as NASA’s primary launch center for human spaceflight since 1968, and since 2013, Jacobs has been helping the space center transition to a 21st century launch facility capable of processing various spacecraft for both private and government entities under a Test and Operations Support Contract (TOSC).
Our team works with the technical community to understand the variables involved in meeting NASA launch dates – getting into everything from how many cranes will be required and how many modifications will be needed on the mobile launcher’s umbilical arms to when the technicians will need to start training onsite to prepare for launch.
But what if we showed you how Jacobs’ proactive maintenance approach is introducing data-driven, cost-cutting and environmentally-sound planning and scheduling of system maintenance and improvements – ultimately preparing KSC to meet its launch dates into the future?
gallons of oil change-overs avoided using a condition-based maintenance approach at Kennedy Space Center
(and counting!) in recorded client cost savings with implementation of trusted oil analysis program and data-driven decision making
“Using predictive maintenance techniques, we have improved connectivity across many contracts and customer organizations. We have integrated commodity life cycles, from procurement through disposal. We’ve also baselined systems early in the construction cycle, so by the time they get into operations, we have a good history to use in predicting future maintenance needs.”
Kevin Berry
Senior Manager, Maintenance & Reliability Engineering, Jacobs Space Operations Group
Images courtesy of NASA
Images courtesy of NASA
Images courtesy of NASA
Just like our vehicles’ maintenance systems have shifted over time – from time-based oil changes to “condition-based” oil changes (think: how your dashboard can predict how much percentage of oil life remains) – technological shifts have led to the ability to advise system engineers about the lubricants in their equipment.
When KSC first awarded us the TOSC to support its modernization efforts, our previous experience implementing a comprehensive oil analysis program for another aerospace client helped us readily conclude the benefit of developing a similar program for Kennedy’s infrastructure and procedures.
The team envisioned improvements to the way lubricants were received, stored, transported, tested and analyzed; while also anticipating that implementing best practices would align to all customers’ needs. We knew that oil analysis would provide the necessary insight on all TOSC assets to optimize the maintenance program of the ground support equipment, and we named the new program the Oil Pharmacy because it established an easy, accessible, one-stop-shop offering solutions for every service.
Within the first two years, we executed changes involving storage and distribution, including inventory consolidation, air-conditioned co-location, procedural documentation creation and the introduction of lubrication codes and a lubrication manual. We piloted the program with one group of system engineers – the Cranes, Doors and Platforms Group – with the intention of expanding to other groups as new procedures were validated. In addition, oil is now kitted in requested quantities in color-coded oil-safe containers dedicated to specific lubrication codes to control contamination.
Today, the TOSC asset management and maintenance & reliability group at KSC operates an award-winning lubrication and oil analysis program that utilizes precision lab equipment and certified personnel to provide on-demand results for real-time analysis and decision making, as well as managing optimized storage with industry best practices. Since 2014, TOSC has recorded more $4 million in cost avoidance achieved due to the implementation of the Oil Pharmacy Program.
Designed in-house and based on industry best practices, the oil analysis lab – one of the major program components – is conveniently located within the storage area and is equipped to diagnose fully the health of lubricants and the assets that use oils.
The Oil Pharmacy lab receives oil samples from all TOSC system engineering groups requiring machine lubrication, analyzes each lubricant for wear, contamination and chemistry composition, and then provides reports to the system engineers with recommendations on how to act on the results. In addition, the lab analyzes all oils as they arrive from suppliers before being added to inventory, oils sitting in storage for other contracts or upon oil delivery to large, critical machines.
Analysis employs a combination of particle counting (utilizing ISO codes), elemental spectroscopy (individual metals in parts per million worn from moving parts as well as contamination and additive element levels) and wear density (wear particle concentration, percent ferrous, micrograms per ml, wear index, etc.) to ensure all large and small particles are recognized. As part of the program, all assets were loaded into Emerson’s OilView software, with limits applied consensually with system engineers, OEM direction and drawing requirements. The team uses Maximo to track asset hierarchy, baseline asset information, condition assessments, labor time and material cost, along with details on oil sampling routes, grease caddy inspections and reporting. In addition, comprehensive reports are provided directly to the system engineers responsible for the asset.
This periodic analysis and assessment is a best practice in the monitoring of asset health and ensures oil is only changed when the condition warrants it – extending the life of oil, preventing unnecessary oil changes and associated costs, reducing environmental impact and increasing productivity.
The procedural changes implemented through the Oil Pharmacy have enabled the maintenance & reliability group to support system engineers in switching from a time-based maintenance schedule to a proactive CBM posture. This conversion has significantly optimized the TOSC maintenance program. Additional positive achievements of the Oil Pharmacy – all indicating that the anticipation of streamlining machine efficiency, control and reliability was well-placed – include:
The Oil Pharmacy program made it possible for analytical findings to be used in data-driven, cost-cutting, proactive decisions for planning and scheduling of maintenance work orders at Kennedy. The TOSC Lubrication Program won ReliabilityWeb’s Uptime Award for Best Lubrication Program in 2016 and was presented with the Augustus H. Gill Award through the International Council of Machinery Lubrication in 2018 for exhibiting excellence in the application of oil analysis in machine and lubricant condition monitoring.